OMV is etting crude oil back out of plastic
Plastic is multitalented! It can be hard as steel, supple as a reed, light as a feather, clear as crystal and much more. It is impossible to imagine our daily lives without it. And the truly bizarre thing about it? Every day we throw away tons of plastic, although it remains a valuable commodity even after use.
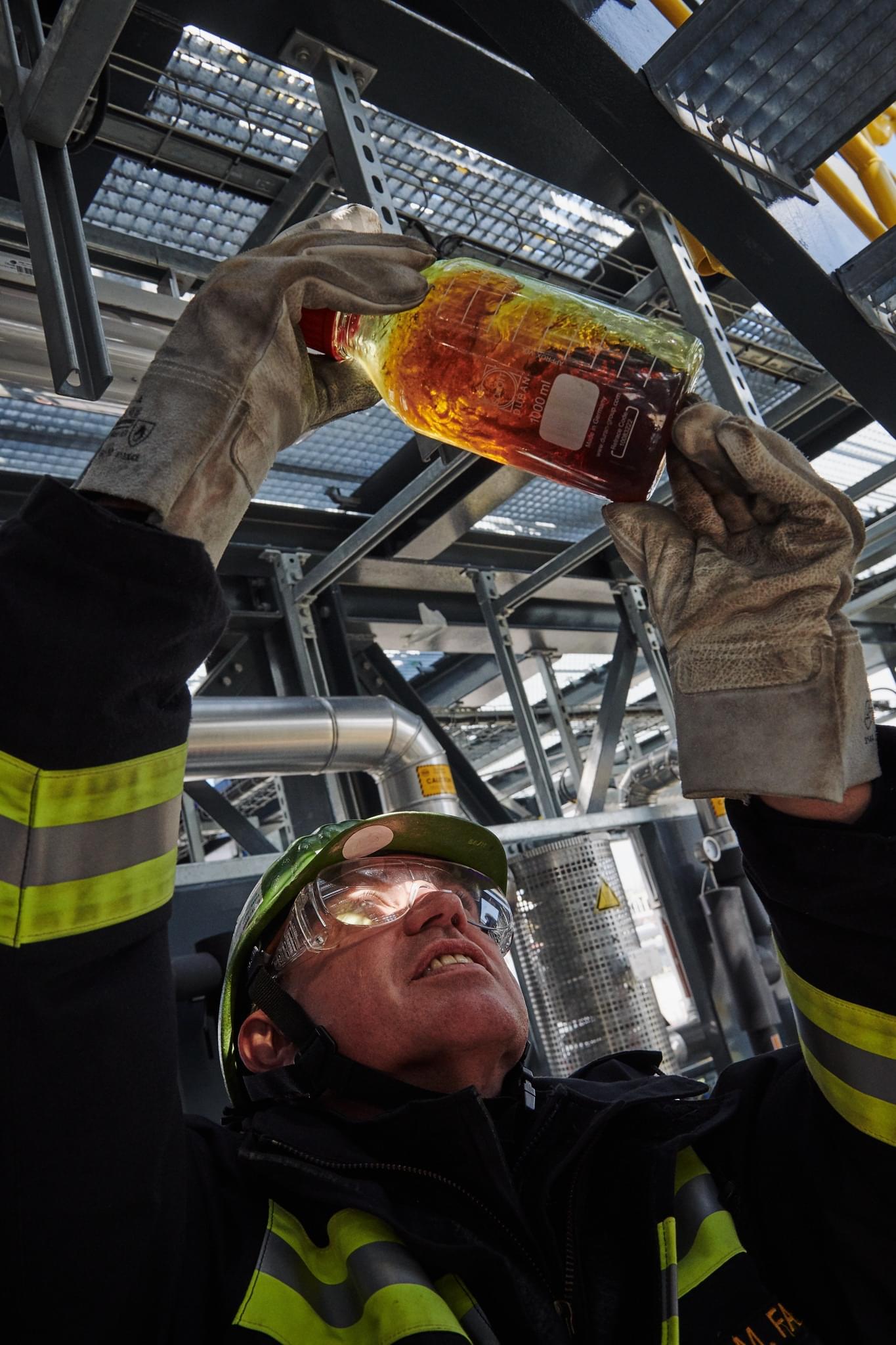
ReOil Anlage Raffinerie Schwechat
Plastic is garbage!
It takes ten to 20 years for plastic wrapping from a piece of fruit to biodegrade, making it fatal to simply throw plastic away. So wouldn’t it be great if you could turn the production process on its head and produce recycled crude oil from plastic waste? There are just a few challenges to overcome first.
Plastic is crude oil!
In order to extract the oil, plastic needs to be heated to over 400 °C. At this temperature, the long-chain molecules from the plastic are cracked and produce synthetic crude oil. Sounds feasible in theory, but it is trickier in practice. After all, plastic is a poorer conductor than glass, ceramics or metal (you can directly pick up a plastic cup filled with coffee), so how can you get the necessary heat into the used plastic? This is a problem that Wolfgang Hofer has been exploring for years while pursuing new technology and feedstock solutions for the refinery. In 2010 he had a brainwave on how to efficiently extract a highly valuable oil from the plastic.
“It would be better if we could convert old plastic into synthetic oil and use this resource either for producing new plastics or as energy for mobility. That would give us a circular economy for plastics, similar to paper.”
Wolfgang Hofer
Senior Expert New Technology, OMV Schwechat Refinery”
Plastic is cyclical!
This brainwave was the starting signal for ReOil. Three years later Wolfgang Hofer and his team had already managed to start up the first test facility in the technology center in the Schwechat Refinery. For ReOil there was also no way of getting around the heating of plastic waste. But then a liquid solvent that solved two problems in one fell swoop came into play, as the engineer explains: “This solvent is part of a cycle in the unit, meaning that it’s already hot. It is mixed with the plastic right at the start of the process, supporting the heating stage and reducing the energy needed thanks to better heat conductivity. What’s more, pure plastic would be too tough to transport through pipes. Adding the solvent also enables us to address this problem.”
After it has been melted down, this mass is vaporized into gas, whereby the long chains of molecules are broken down. They are then subsequently reassembled into smaller chains via chemical processes. In principle the crude oil has now been recovered.
Plastic is research!
After three years of research Wolfgang Hofer’s team produced such good results that more ambitious targets were set. A significantly larger ReOil plant went into operation at the start of 2018 with 20 times the capacity. It is no longer housed in the technology center, but has been given a fixed spot in the refinery between the usual facilities. Michael Fadler is responsible for its operations. “The quality of the products from the ReOil process was already outstanding with the unit in the technology center and that’s something that hasn’t changed. At the end of this we get such a pure, high-quality product that it can hold its own against the best crude. That’s why the new, larger unit is also directly incorporated into the refinery. What we produce here will be used in the production of fuels and other refinery products.”
The new ReOil unit can process up to 100 kilograms of plastic per hour. In the end around 100 liters of valuable crude is secured from 100 kilograms of waste.
Watch our video to find out precisely how the process works and how OMV managed to bringt its research project to the next level.
Related news
Mol and the University of Pannonia have completed a successful consortium project
Mol and Pannon University have concluded a successful consortium project…
Read more >There is a little scepticism about corporate sustainability
According to the Capgemini Research Institute’s 2024 survey, consumer confidence…
Read more >Sustainable packaging: focus on recycling and the circular economy
Packaging is a key element of the supply chain, where…
Read more >Related news
Lidl has published its 3rd sustainability report
Lidl Hungary’s sustainability report for the 2022/2023 business years has…
Read more >Wienerberger donated ten million forints worth of roof tiles for the construction of the Tábitha Hospice House in Törökbálint
The “Being Good is Good!” fundraising activity has been launched…
Read more >Auchan offers its regular customers extra shopping opportunities after closing
Auchan is offering a special shopping opportunity to its regular…
Read more >