With Siemens solutions, the cola factory became more efficient, greener and more transparent
In the Coca-Cola factory in Austria, the introduction of an energy management system built with the help of Siemens greatly contributed to the reduction of energy costs, in addition to its use, losses were reduced, water consumption was reduced and, thanks to careful attention, the amount of loss is also lower than before.
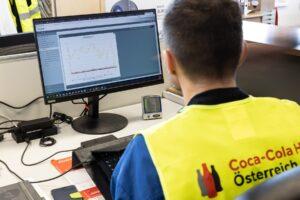
(Photo: Siemens)
Soft drinks produced by Coca-Cola are well known and loved worldwide. In the production unit located in Edelstal, Austria, the manufacturer strives, as in its other plants, to produce high-quality products using the most modern technology possible. For this, it also calls on the tools of automation, production monitoring and energy management. In addition, intelligent condition monitoring within the factory supports production continuity, as real-time monitoring of machines and production lines allows engineers to be aware of blockages, possible breakdowns, and can even be prepared if some maintenance task needs to be carried out in the near future. .
Investing in the future
At the cola manufacturer, emissions are reduced by reducing energy consumption, but this does not come at the expense of efficient production. One of their fastest production plants operates in Austria, where 12 bottles of soft drinks are made per second on the filling line. The investment in the machines operating on the production line was a one-time, large expense for the company, but it already results in significant savings in the short term. In addition to the lower energy consumption, the use of water has decreased, as the bottles waiting to be filled are partially cleaned with air. The compressor that produces the air used for bottle blowing was replaced with a lower-consumption one, so an additional 5-8 percent energy savings are achieved there as well.
System monitoring and reporting
Coca-Cola developed its own energy monitoring system, which had already been introduced at the Austrian plant. However, this had several limitations, so the factory recently turned to Siemens to find a monitoring solution that would allow for more detailed reports and faster data extraction. For this, the Simatic WinCC V7 system was chosen, which is also a huge help in the simple display of measurement data. In the end, the complete monitoring of the energy system was entrusted to the Simatic Energy Manager Pro application, which was deemed flexible and customizable by the plant’s experts. The field measuring devices were supplemented with consumption meters, which were connected to the Simatic ET 200SP system. The collected data is channeled into the monitoring system: this means a total of more than 100 energy and 17 water consumption measurement points, which provide data to the system every minute. The next level of integration is the connection with the company management system, which means easier processing and contributes to the manufacturer getting an idea of the energy and raw material costs of individual products in the factory. All these reports become available in less than an hour, as a detailed overview can be created from the processed data thanks to the complex system. In addition, the information is available not only at a central station, but also from a web application, if necessary, remotely, which makes the operation easier and more transparent for everyone in charge.
Green energy and environmental damage reduction
The company is committed to reducing its environmental footprint, a previous step in this was to provide the factory with 100 percent renewable energy for production. This was then supplemented with measures to increase energy efficiency, and now the update of the monitoring system offers another opportunity for more economical operation. Thanks to these efforts, the amount of carbon dioxide used in the production of one liter of soft drink has been halved. By 2019, this indicator had fallen to 17.5 grams, which is 50 percent less than in 2010.
Health check for efficiency
Condition monitoring provides an opportunity to formulate energy goals and contributes to their achievement. And thanks to intelligent monitoring, unplanned shutdowns that can interrupt production can be minimized. Artificial intelligence plays a role in the scheduling of maintenance and also makes it easier to stock parts. Sitrans SCM IQ reliably warns of potential failures before they occur. However, this requires a built-in and carefully designed signaling system. This system consists of three pillars: Sitrans M200 Multisensors placed on the machines, Sitrans CC220 industrial gateways and the Sitrans SCM IQ application in MindSphere. The sensors collect vibration and temperature data, which clearly show the state changes of the machines and from them we can also infer possible malfunctions. The task of the gateway is to process, encode and transmit incoming data. As a leading IoT solution, the application is responsible for analyzing information and supporting production with forecasts. The energy efficiency and production monitoring systems implemented in Coca-Cola’s Austrian plant also bring lasting and financially demonstrable results to users. With the help of the system solutions put together by Siemens, they can not only receive instant status feedback on the operation, but also make it possible to plan the necessary maintenance. Thanks to this, in addition to reducing energy costs, production becomes more efficient and predictable.
Related news
Pernod Ricard partners with Dole in RTD tie-up
The Malibu & Dole Ready-to-Drink Cocktails range is being produced,…
Read more >YouGov Brand Footprint 2025: the favourite FMCG brands of shoppers
YouGov Brand Footprint is one of the world’s most comprehensive…
Read more >Ágnes Topor: “Many are unaware of the sales-boosting effect of vouchers”
The present economic conditions are negatively affecting consumers, manufacturers and…
Read more >Related news
Danone lines up yogurt facility expansion amid “explosive growth” in US
The Activia brand owner has made a “multi-million dollar investment”…
Read more >Denmark plans to scrap taxes on coffee, confectionery
The complete removal of taxes on coffee and confectionery is…
Read more >Katalin Neubauer: margin stop and mall stop do not serve the interests of retail
The government has extended the margin cap and tightened the…
Read more >